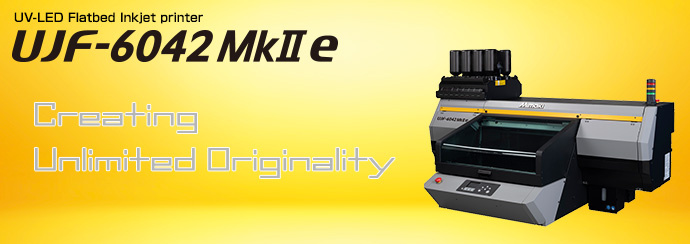
MIMAKI (THAILAND) CO., LTD.
01/31/2025 Information
New post has been published on "Case Study (Mimaki user stories)": Nisso Support System Co., Ltd. : TS55-1800, UCJV300-160, UJF-6042MkII e etc.01/31/2024 Information
New post has been published on "Case Study (Mimaki user stories)": DORAMA Inc. : JV330-16011/22/2022 Information
New post has been published on "Case Study (Mimaki user stories)": DAIDOHBAGS : UJF-6042MkII e"JV330-160" is used for in-house production of goods: DORAMA Inc.